A Custom Bi-Plainer Conveyor Chain Solution for Abattoirs
A focus of Chain & Drives is to provide excellent customised conveyor chain products to our local customers across various industries, including agriculture, constructions & livestock, ensuring seamless integration.
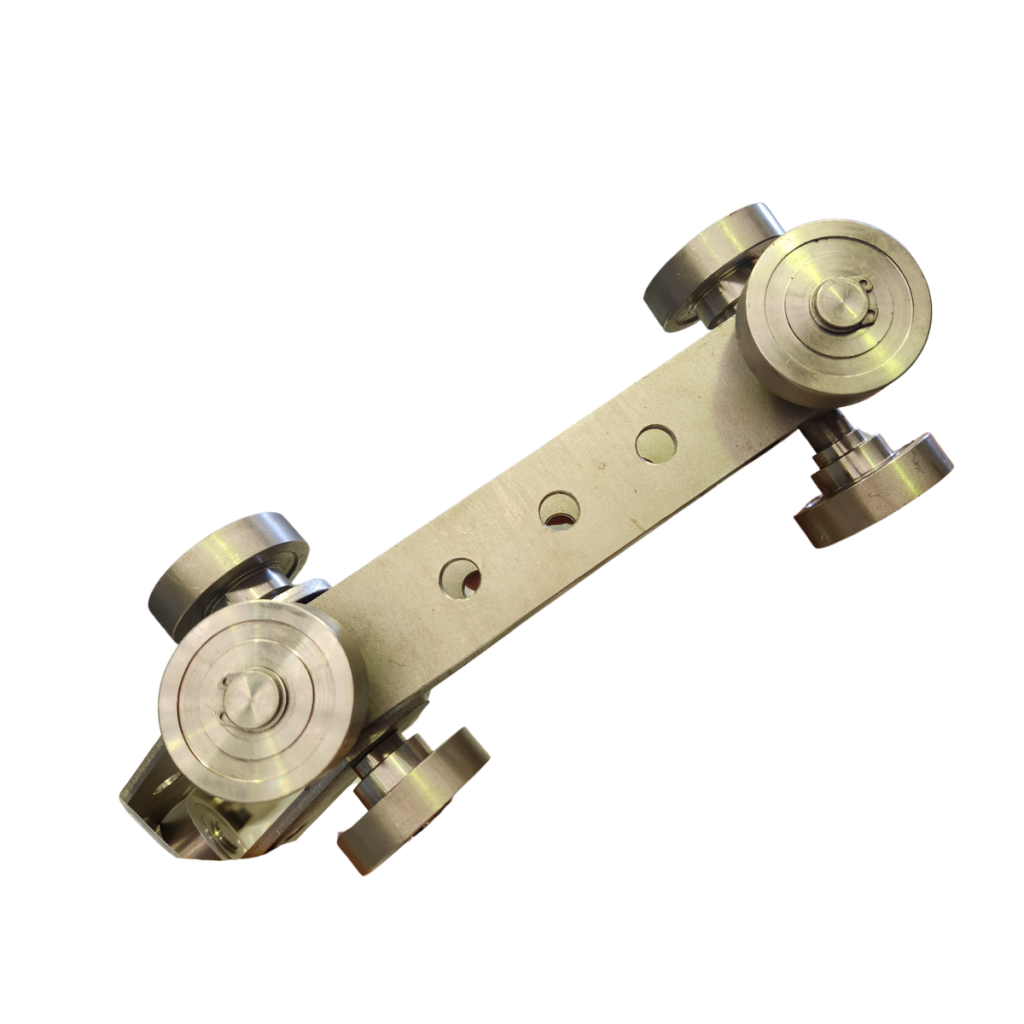
Chain & Drives specialises in providing customised engineering solutions across various industries, including agriculture, construction, and livestock. This case study focuses on a specific project where Chain & Drives, in collaboration with TransDrive, supplied a customised stainless steel bi-plainer conveyor chain to an Abattoir in Albany, Western Australia.
Problem
The WA Abattoir required a specialised conveyor chain to enhance their operational efficiency. The project involved designing and supplying a stainless steel bi-plainer conveyor chain tailored to the abattoir’s specific needs. This type of chain is known for its ability to handle high loads and provide precise control over material movement, making it ideal for demanding environments like abattoirs.
Solution
The customised chain from India was engineered to meet the unique requirements of our customer in the livestock industry. The key considerations in the design process included:
- Material Selection: Stainless steel was chosen for its durability & resistance to corrosion, which is crucial in the harsh conditions of an abattoir.
- Load Capacity & Speed: The chain was designed to withstand heavy loads & operate smoothly at the required speeds, ensuring efficient material handling.
- Environmental Conditions: The chain had to perform reliably in the specific environmental conditions present at the abattoir, including exposure to moisture and varying temperatures.
Collaboration with TransDrive
As a distributor for TransDrive, we leveraged their partnership to source the necessary components and expertise for the project internationally. This collaboration ensured that the chain met the highest standards of quality & performance.
The SS bi-plainer conveyor chain was specially designed utilising 3D imaging technology to ensure optimal performance and seamless integration into the client’s existing production line. This innovative approach allowed engineers to create a highly customised solution that addressed specific operational challenges, allowing the team to visualise the chain’s interaction with other components of the conveyor system, identifying potential issues and making necessary adjustments before manufacturing began. This process reduces the likelihood of costly modifications during installation.
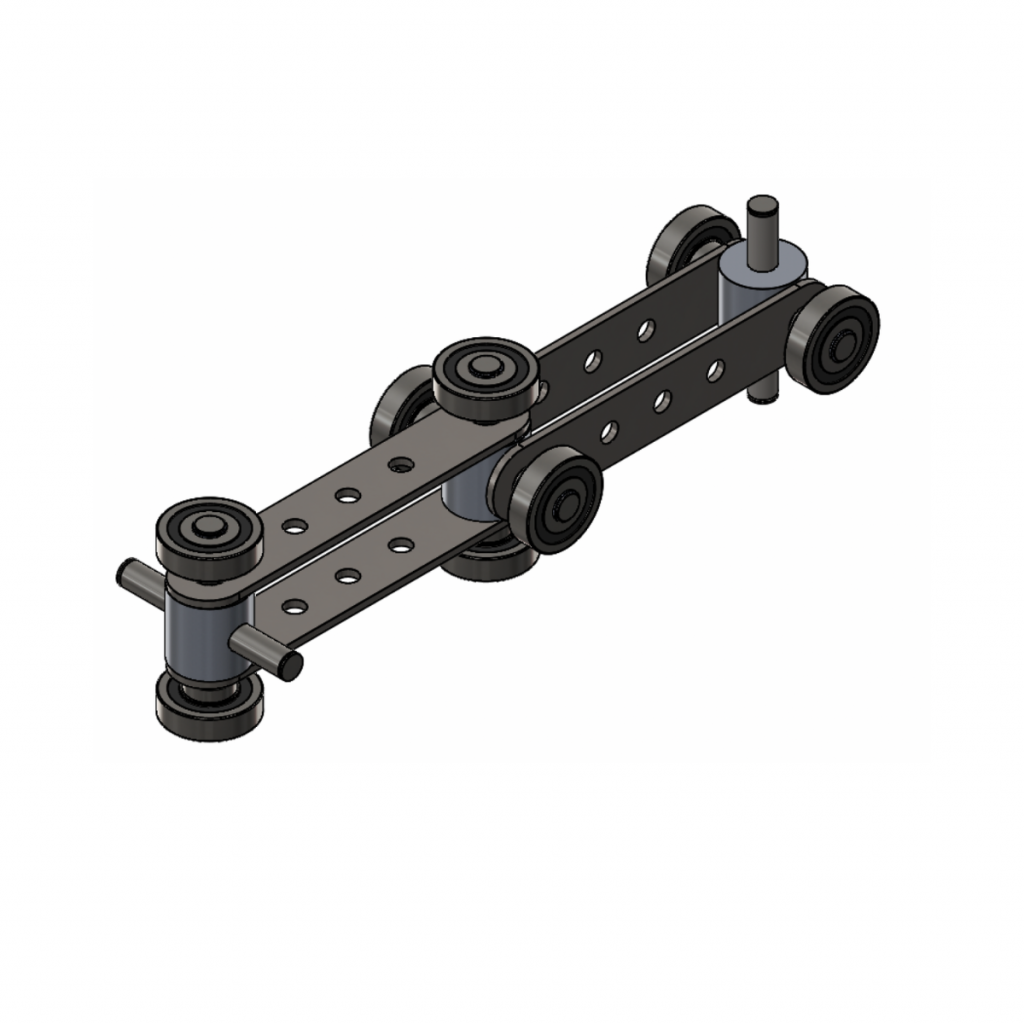
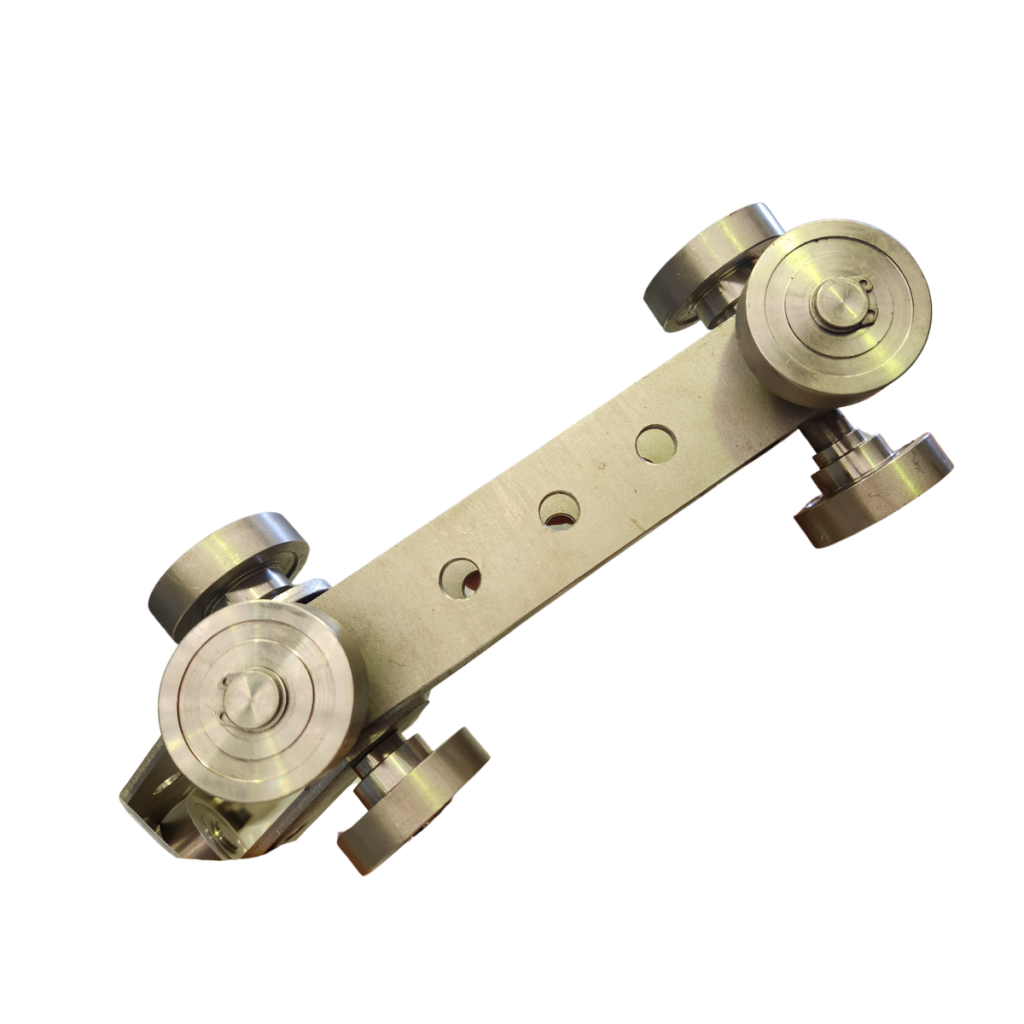
Outcome
The customised stainless steel (SS) bi-plainer conveyor chain successfully met the operational needs of our customer. It provided enhanced efficiency and reliability in their material handling processes, contributing to improved productivity and reduced downtime.
This case study illustrates our capability to deliver tailored engineering solutions by combining their expertise with strategic partnerships. The successful implementation of the customised conveyor chain for a local Abattoir highlights the importance of bespoke solutions in meeting industry-specific challenges.
Contact us today to find out how our customised solutions can enhance your operational efficiency and reduce downtime.
For more information and to discuss your specific needs, visit our website or reach out to our sales team.
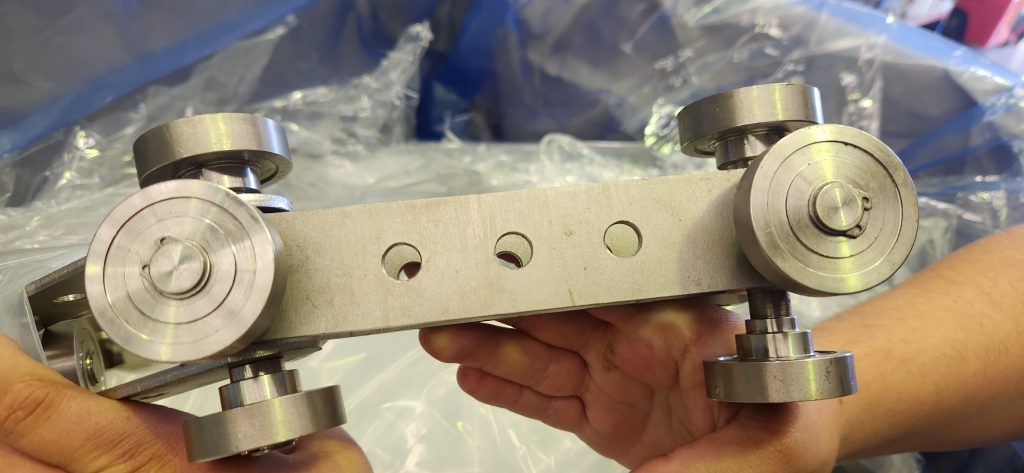
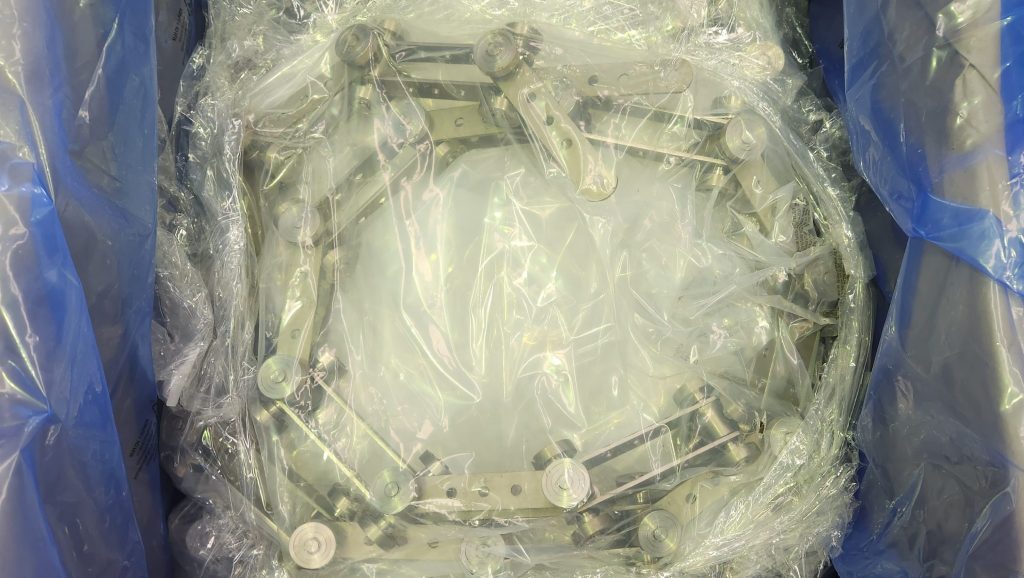
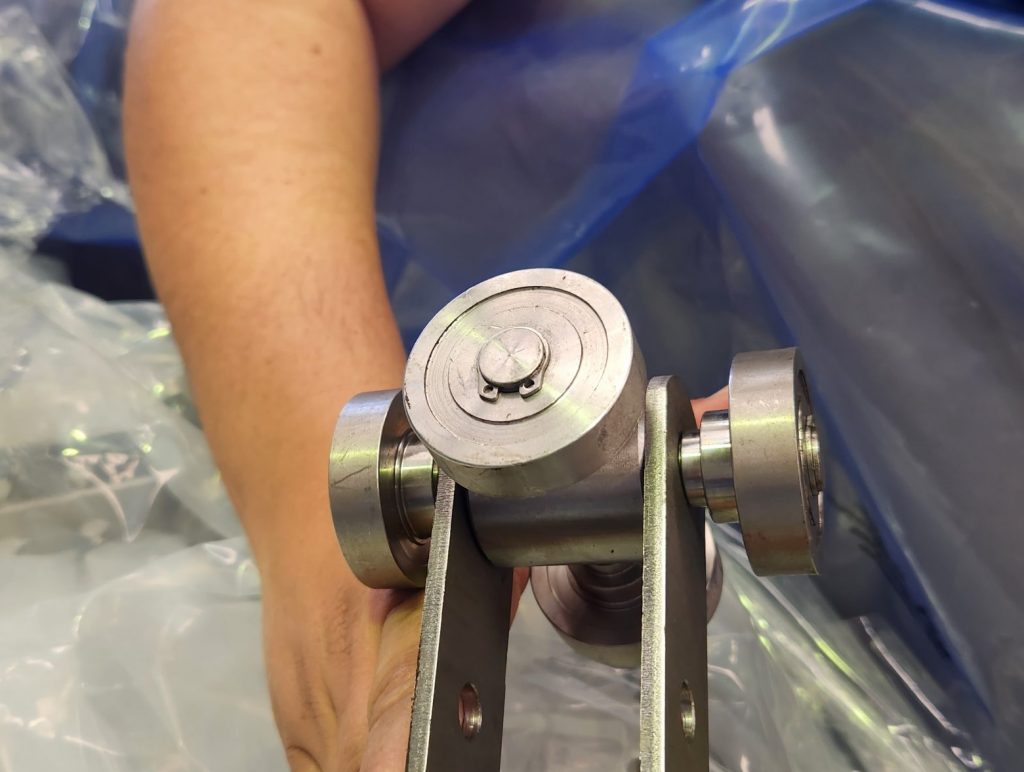
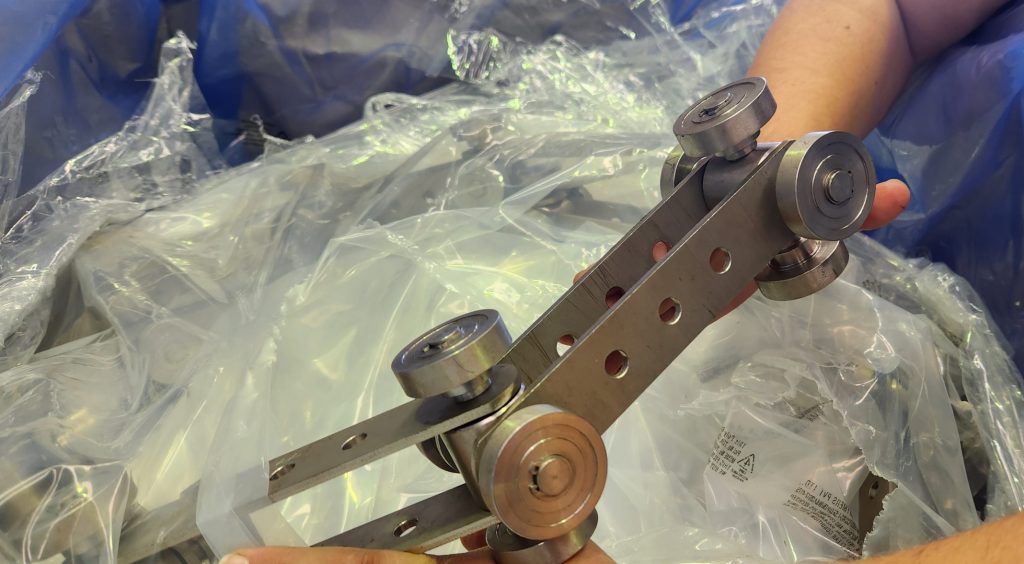
Products
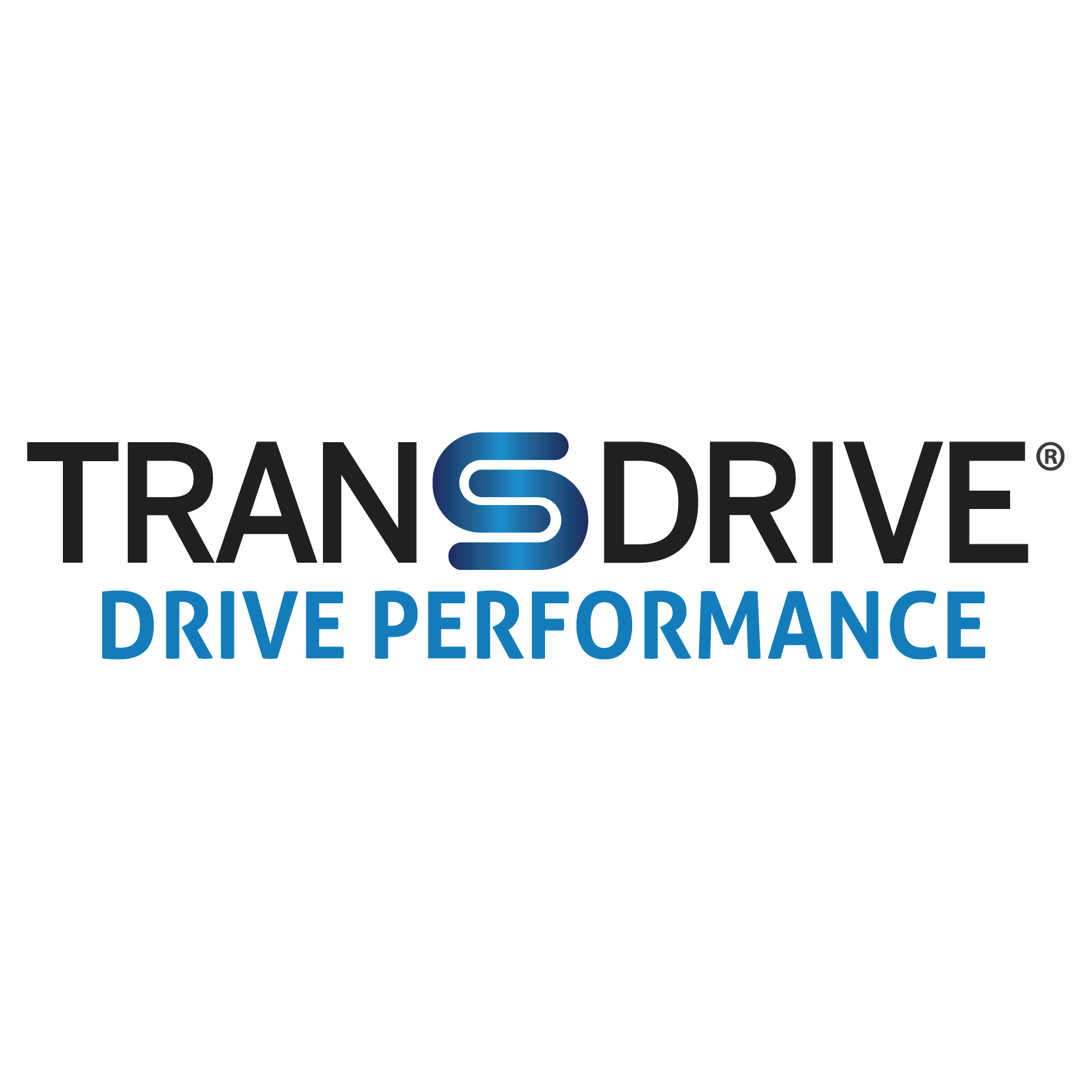